Driver mistakes
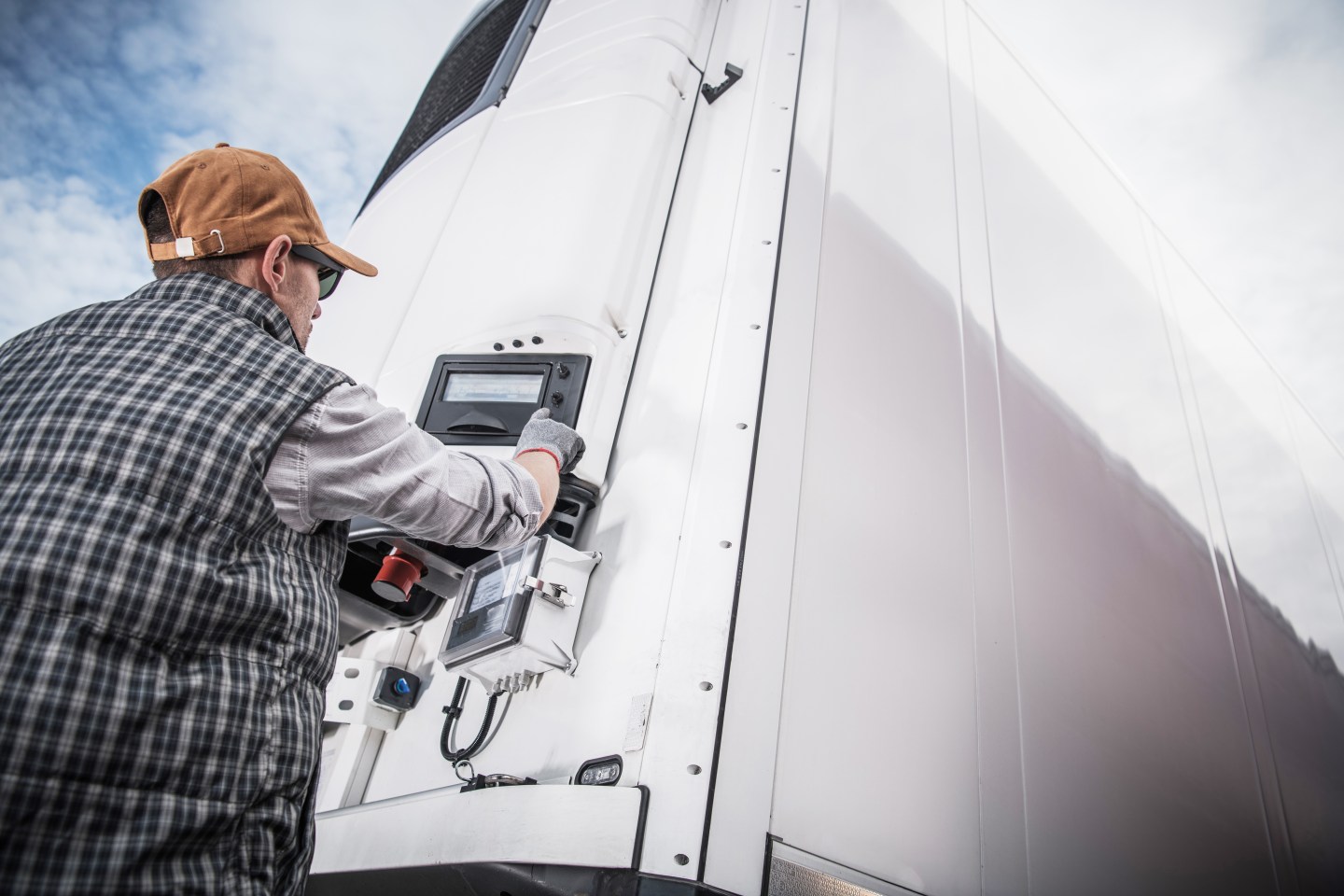
When it comes to managing reefer monitoring operations, driver mistakes are among the top challenges companies must contend with. Reefer drivers have many different responsibilities and instructions to follow, so human error is an inevitable occurrence.
Common challenges
Some common reefer driver mistakes are:
- Driver programming errors – Reefer trailer programming settings are important, and can unfortunately be an area of concern when it comes to driver error. As an example, if a driver accidentally programs a trailer to start and stop instead of continuously run, it could mean damage to the cargo in the trailer.
- Unfamiliarity with reefer alarm codes – Reefer trailer drivers must be very familiar with all alarm codes in a reefer system so they can respond accordingly to the specific alarm triggered. Errors can arise when a driver is unfamiliar with the alarm codes and is not able to make the appropriate response.
- Mistakes during visual load inspections – It’s essential to get everything right when it comes to visual load inspections. Drivers of reefer trailers must make sure to conduct visual load inspections, and they must know how to do so correctly in order to avoid potential issues that could have been easily avoided with proper inspections.
The five most effective fail-safes to minimize the risk of cargo loss
Drivers of refrigerated vehicles have a lot on their plates. In addition to driving the load safely, they may be asked to monitor fault codes, pull off the road to double check temperature readings, reprogram their unit, or perform inspections of whether the vehicle can get to and maintain a certain required temperature. Providing ways to take some of these additional duties off the driver’s plate can significantly minimize the risk of cargo loss, and ensure compliant, on-time delivery.
- Driver training and coaching – Driving the vehicle is job number one, and starts with proper training. Drivers should go through extensive training prior to operating reefer trailers, and dedication should be made to ensuring drivers are coached when mistakes are made so they have the opportunity to learn from and correct their behavior. When processes or methods change, all drivers should be promptly and thoroughly retrained.
- Creating an inspection list – Creating an inspection checklist is an excellent way to ensure processes are streamlined and repeatable, and that drivers never forget a step during inspections. Make sure inspection checklists are always kept updated with the most current instructions for inspection. When changes are needed on inspection checklists, this should be treated with urgency and the changes should be made as soon as possible so drivers always have correct instructions.
- Remotely setting temperature and mode as a fail-safe for fleets – Having a dashboard to remotely set and monitor temperatures is an excellent way to take this responsibility off of your drivers and avoid errors when it comes to temperature settings. Motive’s Thermo King integration includes a Fleet Dashboard where reefers can be remotely controlled and users can configure settings like turning zones on and off and changing modes and set points.
- Automatic alerts for temperature issues – Use reefer monitoring technology that provides automatic alerts for temperature issues. Using this technology provides peace of mind with the knowledge that any issue will be automatically flagged. These real-time alerts will help ensure issues are addressed immediately and the appropriate course of action is taken right away by the correct person. Centralizing the response to these alerts, rather than relying on the individual drivers to take action, can improve both productivity and minimize cargo loss.
- Place wireless environmental sensors in trailers to catch hot zones – Another way to reduce human error and ensure that hot zones don’t arise and damage cargo is to invest in reliable technology. Wireless environmental sensors can be placed anywhere in a reefer trailer to capture humidity and temperature levels and catch hot zones.